Just How Defoamers Improve Performance in Production and Production
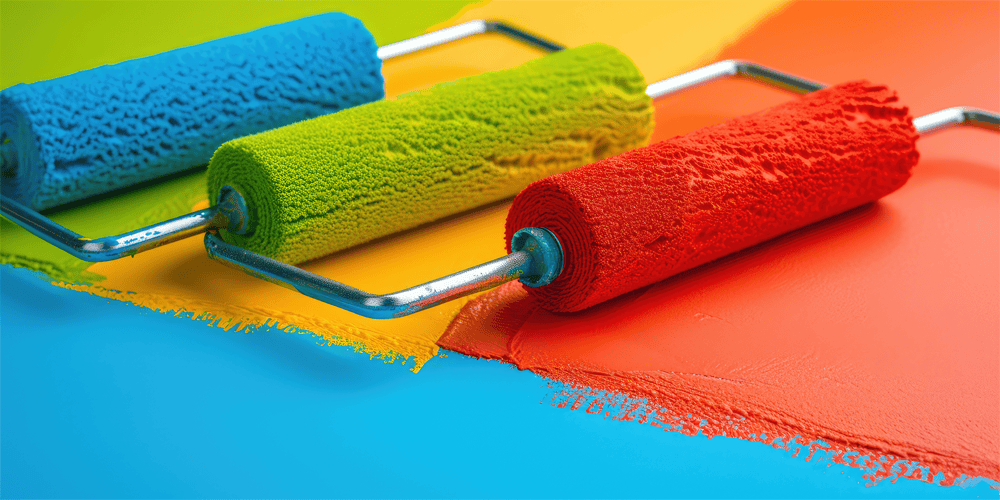
Comprehending Defoamers
Defoamers play a vital role in different manufacturing procedures by properly combating the development of foam, which can disrupt operations and affect item quality. Foam can develop in various contexts, such as throughout mixing, heating, or chemical reactions, possibly causing inefficiencies and incongruities in products. The device through which defoamers run normally includes decreasing the surface area stress of the fluid, permitting bubbles to rise and coalesce to the surface area extra readily, where they can then burst.
Defoamers are developed from a range of chemical compounds, including natural products, silicones, and surfactants, each customized to details applications and procedures. The choice of defoamer relies on aspects such as the kind of material being refined, temperature, and the presence of various other additives. Effective defoamers not just reduce foam formation but additionally keep compatibility with the item, making sure that there are no damaging impacts on the final output. Understanding the residential or commercial properties and features of defoamers is vital for manufacturers aiming to enhance their procedures, improve efficiency, and keep the stability of their items.
Trick Benefits of Defoamers
Making use of defoamers in producing processes uses a range of significant benefits that enhance operational performance and item high quality. One of the main benefits is the reduction of foam formation throughout production, which can obstruct machinery and interfere with operations. By lessening foam, defoamers ensure smoother procedures, causing reduced downtime and maintenance prices.
In addition, defoamers boost item uniformity by protecting against air entrapment, which can endanger the honesty of the end product. This is particularly important in industries where visual look and texture are crucial, such as in paints, finishings, and foodstuff. Enhanced item top quality not only meets client expectations but additionally reinforces brand name online reputation.
Moreover, defoamers can aid in enhancing resource usage. By improving the efficiency of raw product utilization, they contribute to set you back savings and decreased waste, lining up with sustainability goals. Lastly, the application of defoamers can lead to shorter processing times, allowing suppliers to increase manufacturing capability without substantial capital expense - defoamers.
Applications in Numerous Industries
In producing procedures across numerous industries, the application of defoamers plays a crucial role in boosting efficiency and product top quality. These chemical additives are used in industries such as food and beverage, drugs, and textiles to minimize foam-related difficulties.
In the food and drink market, defoamers are important throughout the fermentation process, preventing lathering that can disrupt production and ruin the item's integrity. Likewise, in the pharmaceutical field, defoamers are utilized in the formulation of liquid medications, making certain uniformity and look at this site security while lessening waste.
Textile production likewise takes advantage of defoamers, as they are used in dyeing and ending up procedures to advertise even distribution of chemicals and dyes. This reference application not only enhances the end product's appearance however likewise reduces the amount of water and energy taken in throughout production.
Furthermore, in the paper and pulp industry, defoamers assist preserve procedure performance by reducing foam that can hinder machinery performance. In general, the varied applications of defoamers across these industries underscore their importance in optimizing production procedures and providing top notch products.

Picking the Right Defoamer
Picking a proper defoamer is essential for making the most of effectiveness and top quality in making procedures. The selection of defoamer depends on different aspects, consisting of the specific application, the type of foam being produced, and the formula of the product being produced.

First of all, think about the chemical compatibility of the defoamer with various other components in your formula. A defoamer that communicates negatively with other components can detrimentally influence item top quality. In addition, the temperature level and pH range during processing are essential; some defoamers perform optimally under particular problems while ending up being ineffective in others.
Secondly, evaluate the defoamer's efficiency features, such as its capability to rapidly reduce foam and its persistence throughout manufacturing. It is vital to choose an item that not just eliminates foam rapidly but likewise maintains its performance with time.
Finally, consider environmental and regulative aspects, specifically if your production procedure is subject to stringent conformity criteria. Selecting a biodegradable or low-toxicity defoamer can assist meet sustainability objectives while guaranteeing functional effectiveness. By thoughtfully analyzing these standards, makers can make informed choices that enhance productivity and product integrity.
Ideal Practices for Application
Successful application of defoamers in making processes calls for careful planning and adherence to ideal methods. Initially, it's vital to carry out an extensive assessment of the production setting. This includes recognizing the details application, the types of lathering agents present, and the functional conditions. Choosing the appropriate defoamer, as formerly discussed, is vital; guarantee it is suitable with the materials included and deals with the determined lathering problems successfully.
Following, keep clear communication with all stakeholders, including operators and quality assurance teams. Educating sessions can assist make certain that everybody recognizes the dosing procedures, potential effect on item quality, and safety and security factors to consider. Implementing a test stage can also be useful; monitor performance very closely to assess performance and make essential adjustments.
Furthermore, normal testing and tracking of foam degrees can provide useful insights right into the defoamer's performance with time. Changing does in action to modifications in manufacturing variables will certainly assist keep optimal effectiveness - defoamers. Finally, documenting all procedures and results promotes continuous enhancement, permitting fine-tuning of defoamer use and enhancing total productivity in making operations.
Conclusion
In recap, defoamers play a crucial duty in improving efficiency within production and production procedures. By decreasing foam formation and assisting in bubble coalescence, defoamers add to enhanced item high quality, consistency, and operational performance. Their application throughout numerous markets highlights their versatility and importance in maximizing resource use and lowering handling times. Eventually, the critical application of defoamers allows makers to boost production capability successfully, thus satisfying customer expectations and achieving cost savings.
The benefits extend to item top quality and price financial savings, as defoamers assist enhance procedures.Defoamers play an essential function in various producing procedures directory by efficiently combating the formation of foam, which can influence and interrupt procedures product high quality. Recognizing the homes and functions of defoamers is vital for manufacturers aiming to optimize their procedures, enhance efficiency, and preserve the integrity of their items.
Using defoamers in manufacturing procedures uses an array of significant advantages that enhance operational performance and product top quality.Furthermore, defoamers improve product uniformity by stopping air entrapment, which can jeopardize the integrity of the last product.